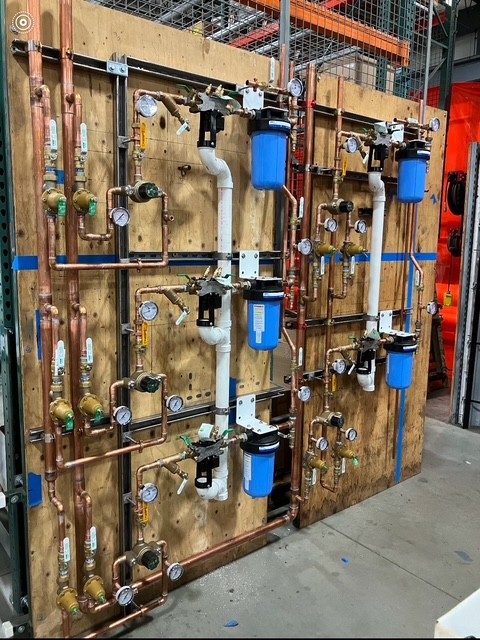
SERVICE LEAD
Alan VanMun, Project Executive
Our fabrication capabilities are driven directly thru utilization of the nearly 150,000 standard components within our FAB Parts software database. By focusing our efforts on Tweet/Garot’s standard assemblies and process automation, we can cut time in both the design process and evaluation of alternative methods. This allows our project team to focus prefabrication efforts on skids and modularization.
Through the utilization of this strategy, we have shifted 40% of plumbing and piping hours to our shop, which in turn reduces the installation schedule and manpower requirements onsite. In addition, this mitigates onsite safety issues and helps ensure QA/QC compliance.
Modular systems are designed with the focus on owner needs and budget.
Quick turnaround in a safe, controlled production environment.
Up front trade coordination minimizes time in the installation phase.
Optimizing efficiency through all phases of design, fabrication and construction.
Upon coordination completion our assemblies and orders are packaged into schedule driven installation kits and follow an orchestrated manufacturing process including a truck loading plan to ensure efficient unloading and staging in key project areas. Each kit comes with a unique installation plan with all dimensional and elevation information to simplify field execution onsite.
Process automation and lean manufacturing is our focus. This allows for the efficient fabrication and skidding of ductwork, piping assemblies, plumbing, and med gas components. From headwall assemblies, pump skids with piping and electrical wiring, to in wall toilet and sink carrier banks, our integrated team will continue to find new ways to connect the model to the shop floor and fabricate offsite.